EXTENSION SPRINGS
A type of spring designed to support tension, or pulling loads. Extension springs are also called tension springs.
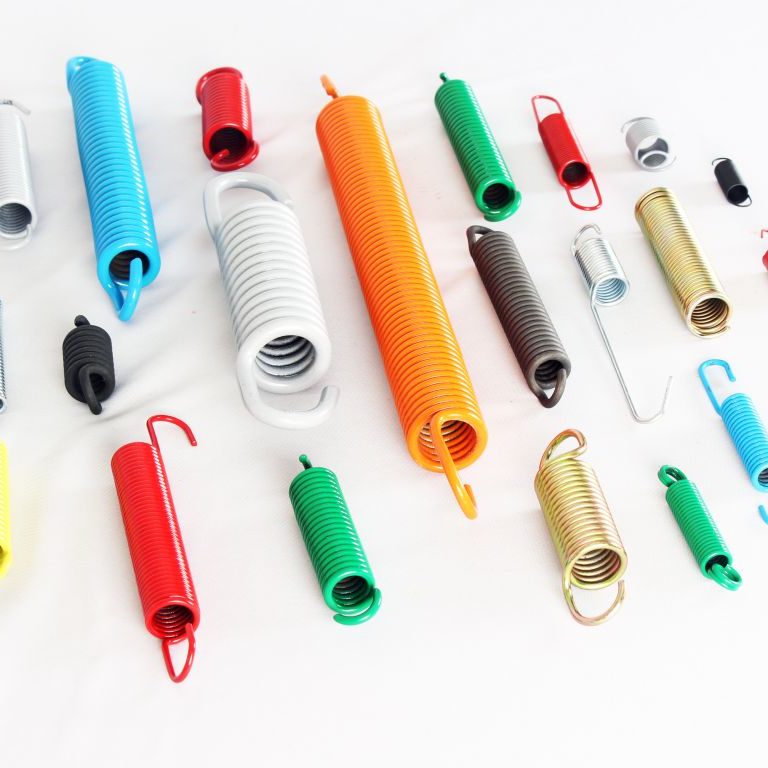
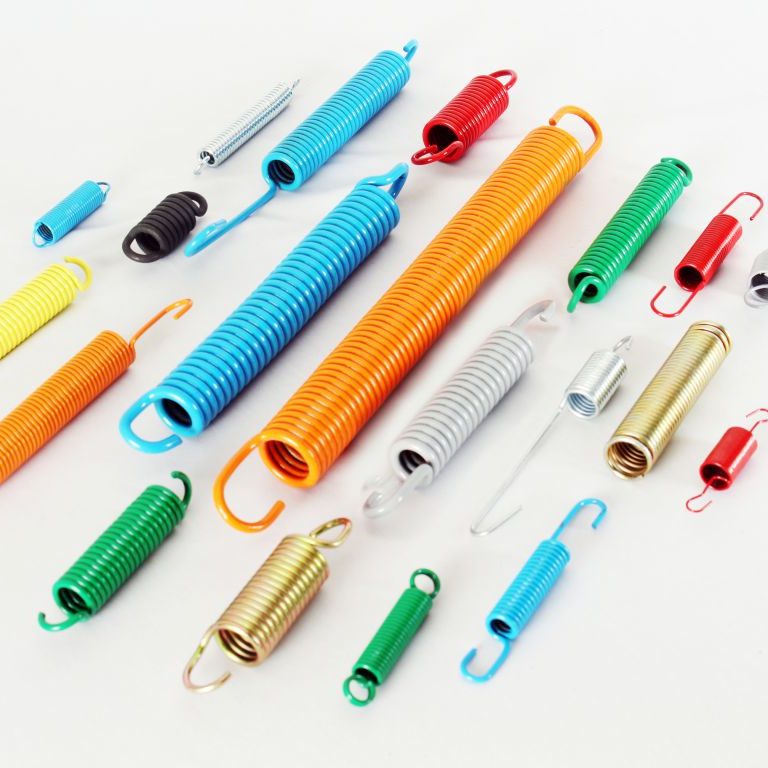
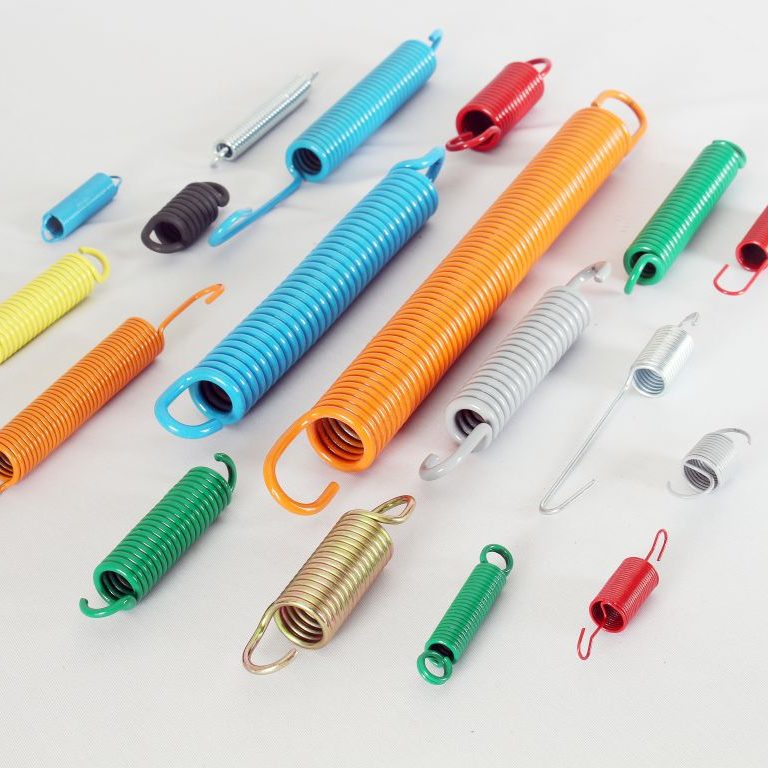
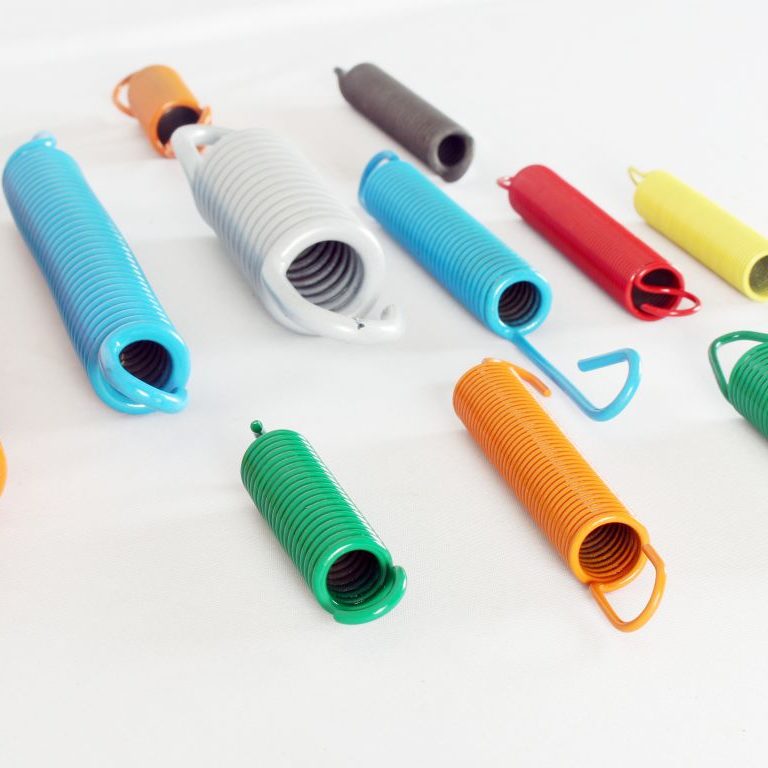
“We manufacture compression springs from Wire dia 0.1 mm to 12.5 mm”
The difference between helical compression and helical extension spring is in the direction of load application and the method by which it is applied.
In order to apply the force, special end form numbers have to be used, either utilizing the formed end coils or special hook.
The more complex the end formation the greater the manufacturing tolerances & greater the manufacturing cost.
How Accurate designs extension springs
- Extension Springs are more expensive than compression springs and should be stressed about 10% to 15% lower to allow for overstretching at assembly and to reduce the stresses in the hooks.
- They should be designed with some initial tension to hold the coil together. Springs without initial tension are difficult to manufacture.
- Do not specify the relative position of the hooks with regard to each other unless it is important. The spring manufacturer may have to vary the position a little to meet the more important force and deflection requirements. Avoid using large, extended or special hooks wherever possible, as they may double to triple the cost of spring.
- Keep the outside diameter of a hook the same as the OD of the spring so that the hook can be made by bending up a regular coil. Do not specify the hook opening with small tolerances. Swivel hooks and coned ends help to reduce hook breakage and are quite expensive.
- The body length or closed portion of an extension spring equals the number of coils in the body plus 1, multiplied by wire diameter.
- Electroplating does not deposit a good coating between the coils nor on the inside diameter, but such springs should not be extended during plating as this causes a higher amount of hydrogen embitterment.
- Heating extension springs to remove residual stresses caused by coiling also may reduce the amount of initial tension by as much as 50%. Allowance for this reduction should be made in manufacturing.
- When two or more forces are specified, they automatically determine the rate and the deflection. Testing for two forces is often expensive, time-consuming & frequently can be avoided by proper design considering normal spring tolerances.