TORSION SPRINGS
The mode of operation of torsion springs is different from compression springs and extension springs. At accurate springs, wide ranges of torsion springs are manufactured on CNC Machines.
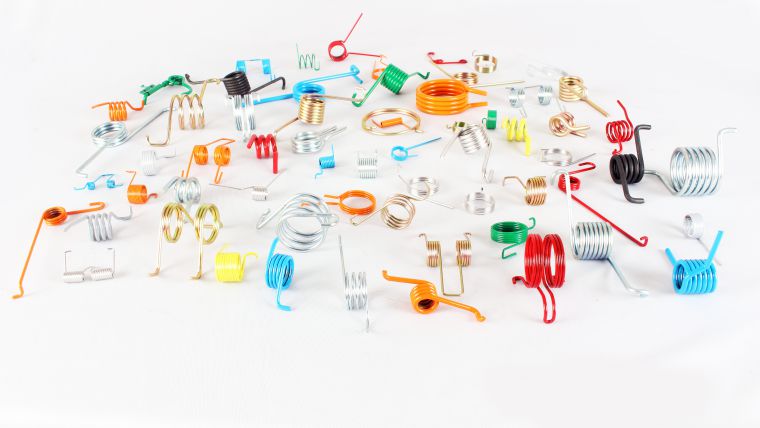
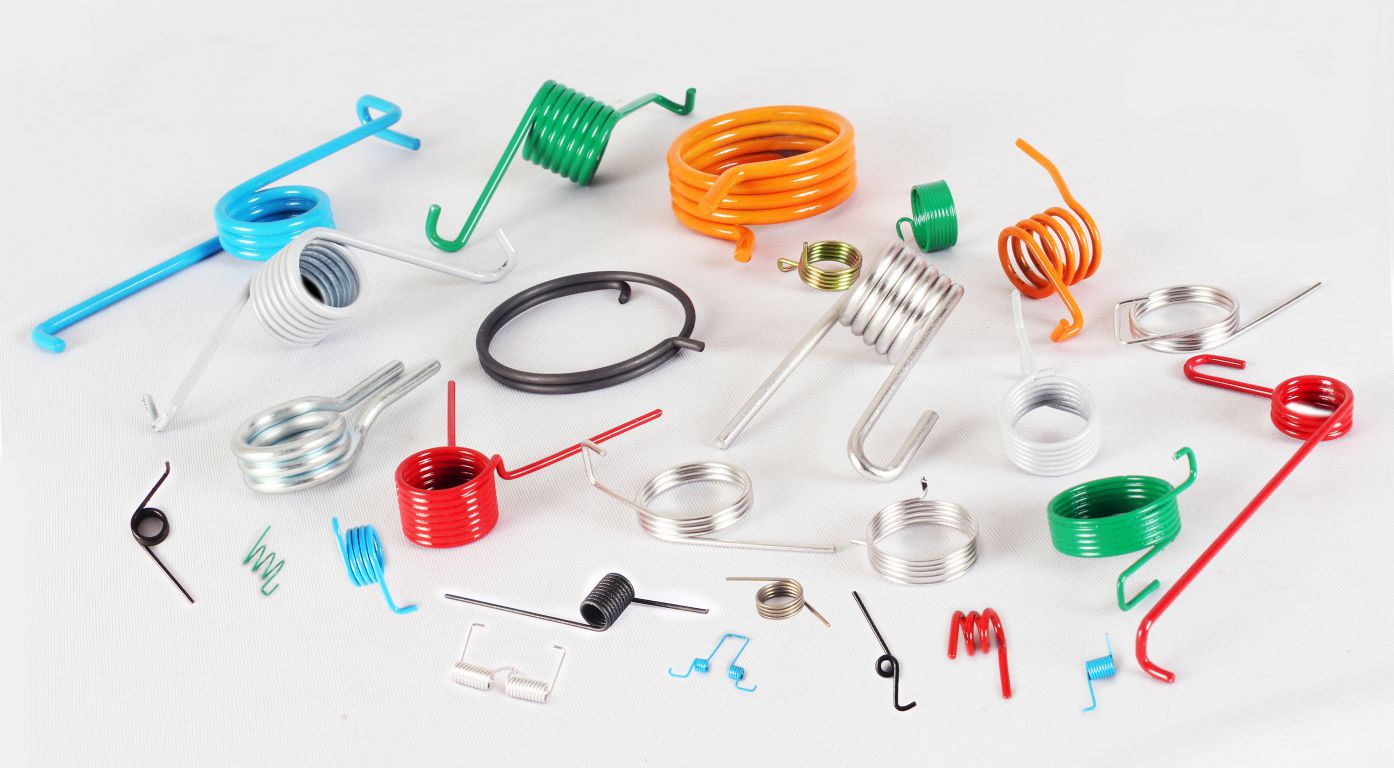
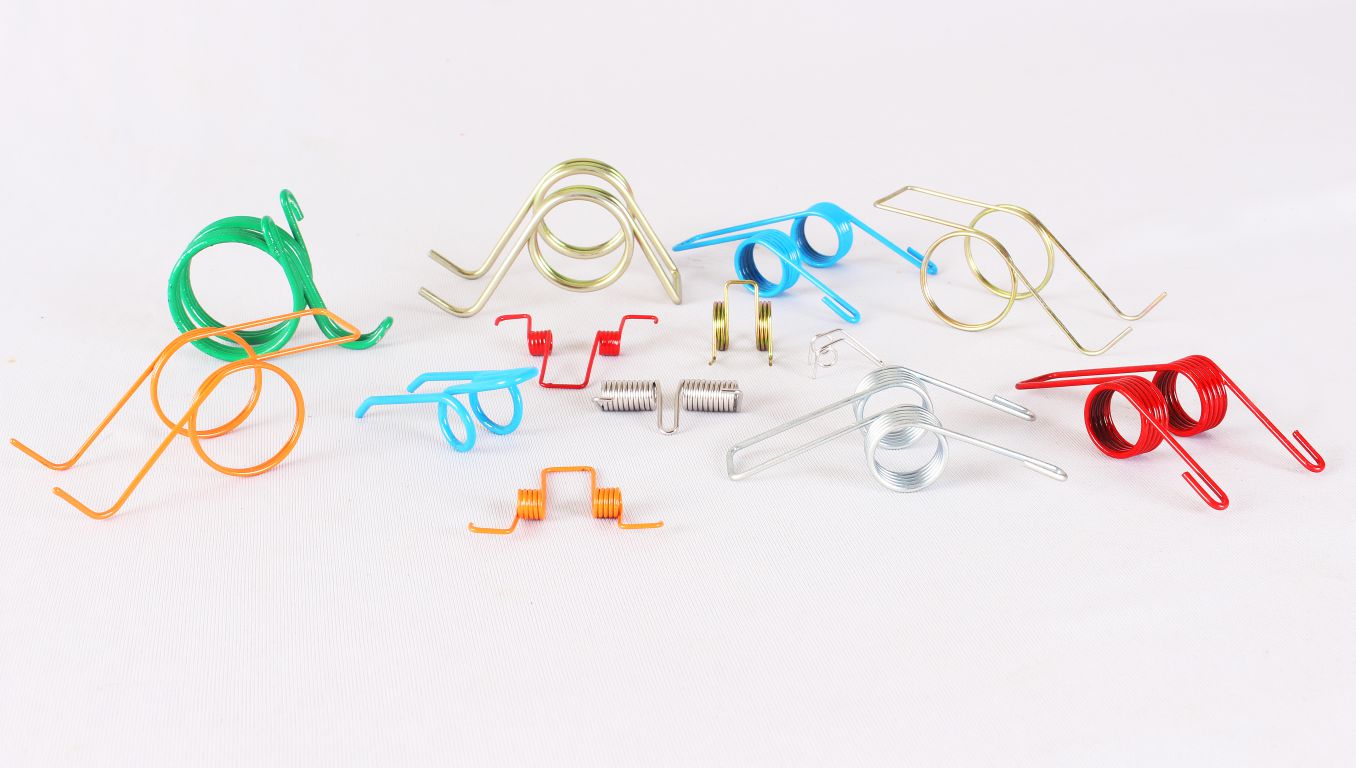
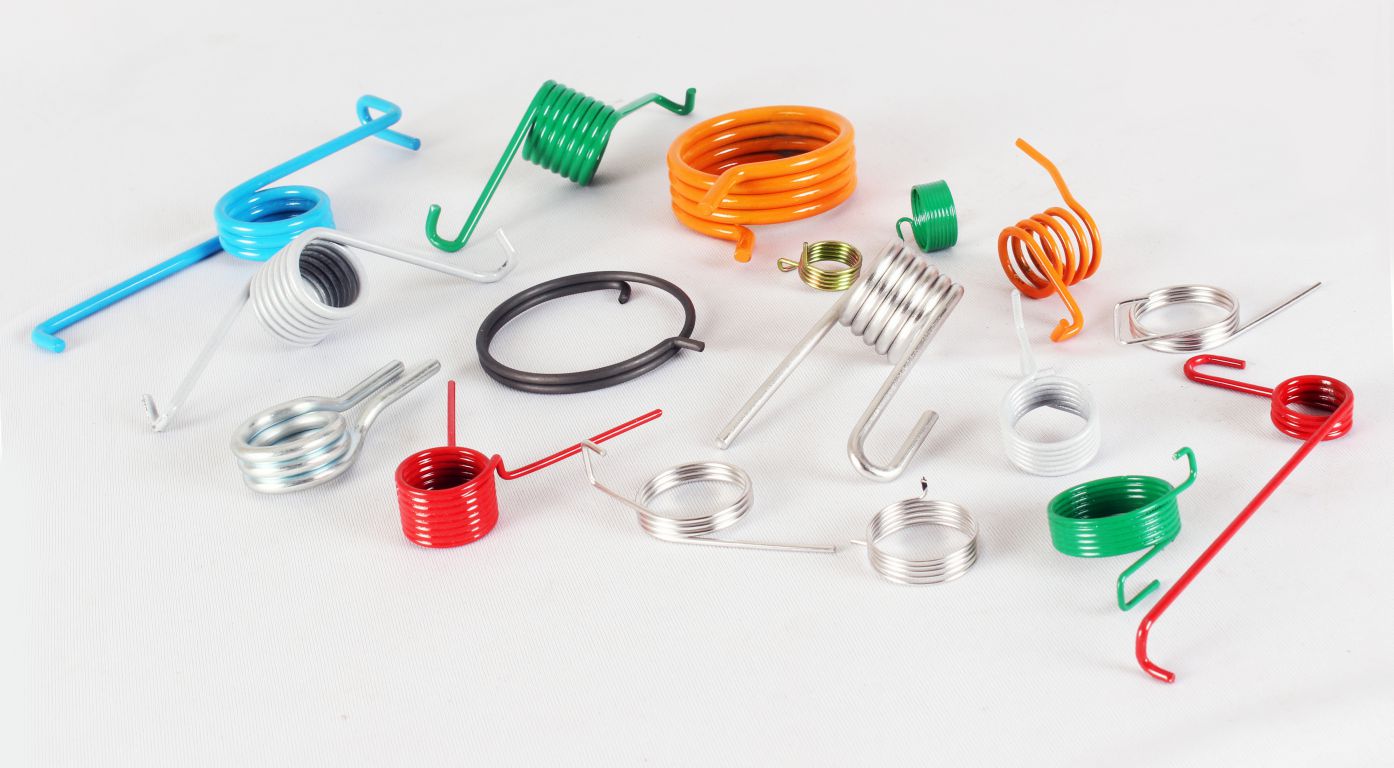
“We manufacture compression springs from Wire dia 0.1 mm to 12.5 mm.”
A torsion spring is, in effect, a wound up cantilever. Torsion springs supply or withstands torque. To supply this torque, torsion springs require some form of spring leg. The type of spring leg is dictated by the application and can be as simple as a tangential straight leg or much more complex. It should be noted that it is best to keep the legs as simple as possible to reduce manufacturing tolerances and manufacturing difficulties.
How Accurate designs torsion springs
- Proportions: A spring index that is a ratio of a mean diameter divided by wire diameter between 4 and 14 is best. Larger ratios require more than average tolerance. Ratios of 3.5 or less often cannot be coiled on automatic spring coiling machines because of arbor breakage. Springs with smaller or larger indexes do not give results exactly as the design formulas.
- Total coils: Torsion springs with less than 3 coils buckle and are difficult to test accurately. When 30 or more coils are used, light loads will not deflect all the coils simultaneously due to the friction with supporting rod.
- Diameter reduction: The inside diameter reduces during deflection. This should be considered and accordingly, clearance should be provided over the supporting rod. Also, allowances should be considered for normal spring diameter tolerances.
- Hand: The hand or direction of coiling should be specified for the spring designed, so deflection causes the spring to wind up and have more coils. This increase in coils and in overall length should be considered during design. Deflecting the spring in an unwinding direction causes high stress and may cause early failure.
- Bends Arms: They should be as straight as possible. Bends are difficult to produce and often are made by secondary operations, and are expensive. Sharp bends are stress raisers that cause early failure. Bend radius should be as large as possible. Hooks tend to open during deflection.